Dans le secteur de la carrosserie et de la peinture industrielle, le grenaillage est une technique essentielle pour le traitement des surfaces métalliques. Il permet d’éliminer la rouille, les résidus de peinture, les huiles et autres contaminants afin de préparer les pièces pour l’application d’un revêtement protecteur. Toutefois, l’un des défis majeurs réside dans la séparation efficace de la grenaille et du sable, deux éléments fréquemment utilisés ensemble lors du processus. Une séparation optimale est essentielle non seulement pour garantir la qualité des opérations, mais aussi pour optimiser les coûts et limiter l’impact environnemental.
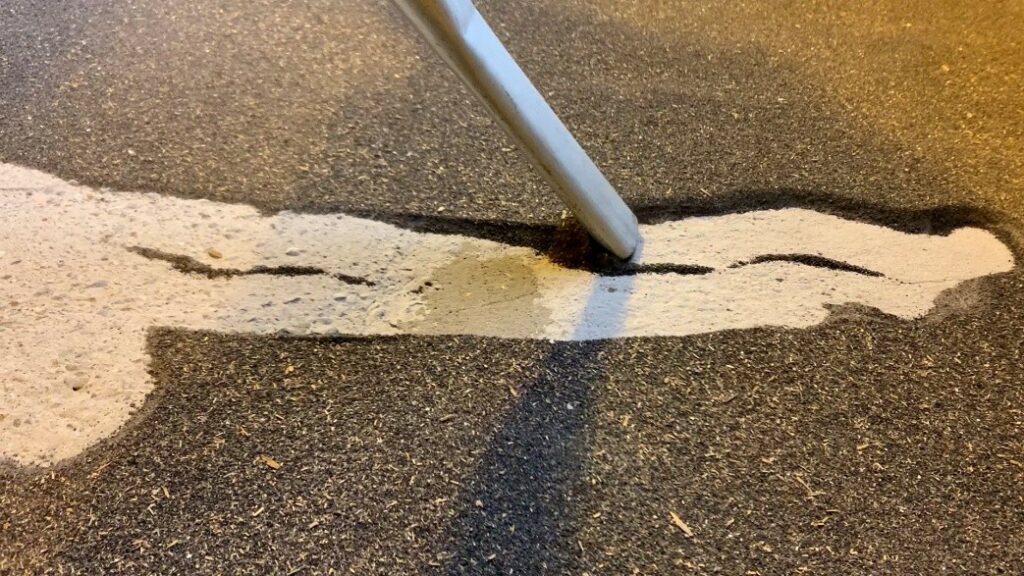
Un défi technique et économique maîtrisé
Le grenaillage est un procédé incontournable pour préparer les surfaces métalliques à de nouvelles applications. Toutefois, l’utilisation conjointe de grenaille et du sable pose plusieurs problématiques. Une mauvaise séparation entraîne une perte de grenaille bien que réutilisable et une contamination du sable, augmentant ainsi les coûts d’exploitation. La manipulation de ces matériaux peut générer des poussières fines, nocives pour la santé des opérateurs et susceptibles d’altérer la qualité du travail. C’est pourquoi, une séparation efficace entre la grenaille et le sable doit être réalisée, afin de garantir une rentabilité optimale.
L’objectif principal du projet était d’atteindre un taux de séparation d’au moins 60 % entre la grenaille et le sable, permettant de réduire les coûts d’achat de consommables et d’améliorer la sécurité des opérateurs. Il était également primordial de garantir un processus simple d’utilisation, afin de limiter les contraintes pour les équipes sur le terrain notamment celles liées à la manutention de la grenaille. D’une densité de 4, la grenaille est un matériau lourd ; pouvant générer d’importants risques TMS pour les opérateurs lorsque celle-ci est déplacée manuellement.
Une solution sur mesure pour un processus optimisé
Pharaon a conçu une solution combinant puissance, efficacité et simplicité d’utilisation, permettant une séparation efficace de la grenaille et du sable tout en limitant l’exposition aux poussières pour les opérateurs.
Nous avons associé la puissance d’un aspirateur industriel à un pré-séparateur cyclonique d’une capacité de 200 litres.
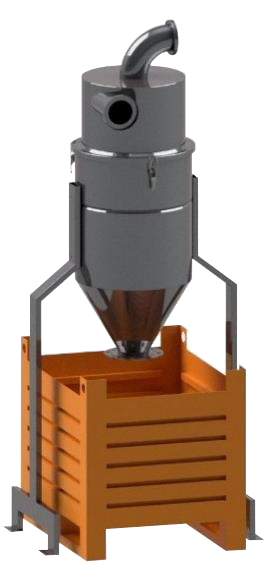
Ce pré-séparateur installé sur châssis fixe, disposé au-dessus de la grenailleuse, permet de récupérer la grenaille et de la réinjecter dans le processus tout en isolant le sable dans la cuve de l’aspirateur. Ce dispositif de 200 litres, équipé d’un clapet pendulaire et d’une goulotte de vidange, garantit une séparation efficace et évite toute dispersion inutile des matériaux.
Nous avons prévu un flexible d’une longueur de 10 mètres permettant aux opérateurs de manipuler l’équipement facilement, au sein de toute la zone de production, sans déplacer les machines, améliorant ainsi leur confort de travail.
Les opérateurs viennent aspirer directement le mélange de grenaille et de sable, plutôt que déplacer les matières manuellement, occasionnant une mise en suspension des poussières dans l’atmosphère. Ces nuages de poussières sont nocifs pour les opérateurs : le sable contient de la silice cristalline responsable de maladies respiratoires, c’est une matière classée CMR de catégorie 1.
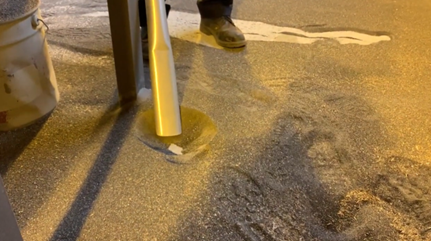
Des résultats concrets et mesurables
La mise en place de cette solution a permis d’obtenir des performances nettement améliorées. Le taux de séparation a été optimisé entre 60 et 70 %, garantissant une meilleure réutilisation de la grenaille et limitant les déchets. La réduction des pertes de grenaille a entraîné une baisse significative des coûts d’achat de nouveaux matériaux.
L’automatisation du processus de séparation a permis d’optimiser le temps de travail des opérateurs, réduisant ainsi les tâches manuelles et les efforts liés à la manipulation des matériaux. La sécurité a également été renforcée grâce à l’aspiration efficace des poussières volatiles, protégeant ainsi la santé des équipes et améliorant les conditions de travail.
Une zone dédiée à la séparation et à la réutilisation de la grenaille a été aménagée, renforçant la fluidité et la performance des opérations industrielles. Ce nouvel espace permet d’optimiser la gestion des matériaux tout en garantissant une meilleure organisation du travail.
Initialement, l’entreprise souhaitait conserver un tamis de séparation, pensant qu’il assurerait un tri efficace. Cependant, les résultats obtenus avec la nouvelle solution ont été si concluants qu’il a finalement été retiré, permettant ainsi une simplification du processus et une réduction des coûts supplémentaires liés à son entretien.
Une approche adaptée aux enjeux industriels
Ce projet démontre l’importance d’une approche technique bien pensée pour optimiser les processus industriels. Grâce à l’expertise de Pharaon en aspiration industrielle et en gestion des matériaux, il est possible d’améliorer l’efficacité des opérations tout en réduisant les coûts et en garantissant la sécurité des travailleurs.
En intégrant des solutions adaptées, les industriels peuvent augmenter la productivité de leurs équipements, et améliorer les conditions de travail des opérateurs. Expert en solutions d’aspiration industrielle depuis 1972, Pharaon accompagne les professionnels dans le choix des meilleures solutions pour leurs besoins spécifiques.